Production
Steel Service Center
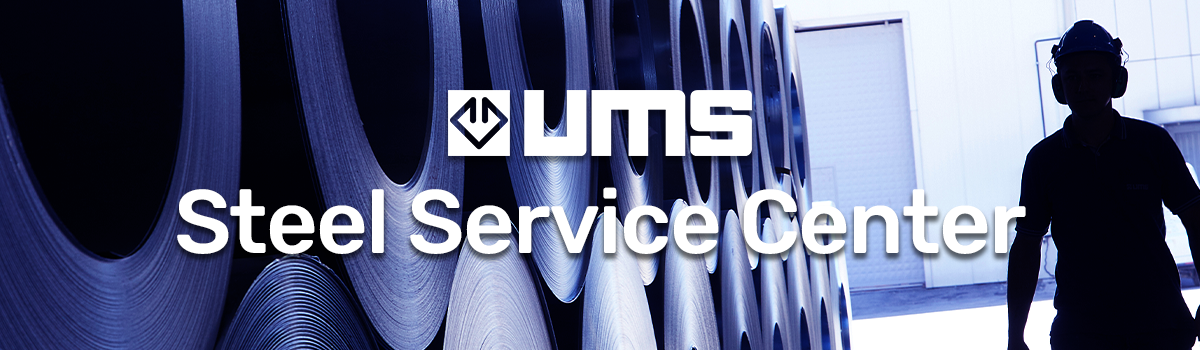
With an annual production capacity of 120,000 tons, UMS is your address for fast and high-quality solutions for your steel needs!
At UMS, the Steel Service Center is a production facility where galvanized and painted galvanized coil sheets, slit coils, flat sheets, and trapezoidal sheets in different forms are produced using raw materials that meet Turkish and international standards.
UMS Slitting Line
This is the production line where coil sheets are slit transversely with circular knives.
UMS Metal Slitting Line Specifications:
Production Capacity | 50.000 tons/year |
Max. Coil Weight | 20 ton |
Min/Max Coil Width | 25/1550 mm |
Min/Max Coil Thickness |
0,25/4,00 mm |
Speed | 150 m/min |
*UMS Slitting Line
UMS Cut-to-Length Line:
This is the production line where coil sheets are cut lengthwise. The cut-to-length line has two straightening units for double straightening purposes.
This allows production with very narrow wave tolerances.
UMS Cut-to-Length Line Specifications:
Production Capacity | 40.000 tons/year |
Max. Coil Weigth | 20 tons |
Min/Max Coil Width | 300/1250 mm |
Min/Max Coil Thickness | 0,25/3,00 mm |
Min/Max Length | 300/10000 mm |
Speed | 50 m/min |
*UMS Cut-to-Length Line
UMS Trapezoidal and Corrugated Sheet Production Line:
This is the line where coil sheets are formed through roll forming into 27/200, 18/76.2, 58/915, 38/151 sections.
UMS Trapezoidal and Corrugated Sheet Production Line Specifications:
Production Capacity | 30.000 tons/year |
Max. Coil Weight | 15 tons |
Min/Max Coil Width | 1000/1200 mm |
Min/Max Coil Thickness | 0,25/1,50 mm |
Min/Max Sheet Length | 300/12000 mm |
Speed | 50 m/min |
*UMS Trapezoidal & Corrugated Sheet Production Line
Profile Production
With 46 production lines, all developed with its own special technology, UMS boasts an annual profile production volume of 150 million meters. The profiles produced are manufactured from raw materials that we produce ourselves, incorporating many unique features and innovations that are exclusive to UMS. In this regard, UMS is recognized as the largest fully integrated production facility in Europe.
Setting the benchmarks in ceiling, exterior cladding, partition, and curtain wall profiles, UMS is constantly innovating and producing cutting-edge products, thanks to its commitment to R&D and innovation. With over 200 product varieties, UMS stands as one of Turkey's largest producers of gypsum board profiles, drywall profiles, and plaster profiles.
UMS Suspended Ceiling, Exterior Wall and Drywall Profiles Production Lines:
Our suspended ceiling, exterior cladding, partition wall, and curtain wall profile products, manufactured with high engineering and technology, meet world standards with TSE and ISO certifications. UMS offers quality, high-strength, and reliable application solutions with unique products such as M Profile, Power, EcoForm, and Light Band U Profile.
Technical Specifications of UMS Ceiling and Wall Profiles Production Lines:
Production Capacity | 150.000.000 m/year (total) |
Max. Roll Weight |
5 tons |
Producible Min/Max Sheet Width |
30 mm / 300 mm |
Producible Min/Max Sheet Thickness |
0,25 mm / 2,00 mm |
Speed |
100 m/min 50 m/min (with holes) |
*UMS Profile Production Lines
UMS Corner Profiles Production Line:
Our plaster and perforated corner profiles, produced with high engineering and technology, are manufactured to meet global standards with TSE and ISO certifications.
Technical Specifications of UMS Corner Profiles Production Lines:
Production Capacity | Corner profile : 18.360.000 m/year Perforated corner profile: 58.752.000 m/year |
Max. Roll Weight | 5 tons |
Producible Min/Max Sheet Width | 29 mm / 35 mm |
Producible Min/Max Sheet Thickness | 0,20 mm / 0,50 mm |
Speed | 20 m/min (corner profile) 65 m/min (perforated corner profile) |
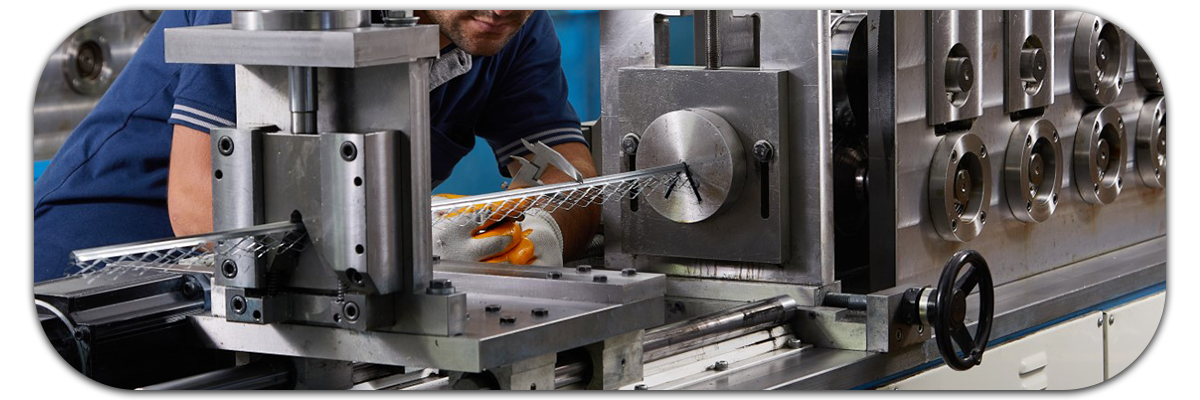
Light Gauge Steel Framing
Production of Light Gauge Steel Framing at UMS
At UMS, we provide accurate structural solutions in accordance with global standards through our skilled design and detailing team in light gauge steel structure manufacturing. Our team ensures that your project's technical and structural design is meticulously prepared, initiating the production process. Subsequently, the required profiles for your project are produced using our advanced and high-capacity machinery. Our assembly team then fastens the produced profiles to perform panel assembly. The completed panels are appropriately transported to the site, assembled, and the project is finalized with on-site installation.
Advantages of Light Gauge Steel Framing
- High Sustainability
- Full Recyclability
- Time Saving
- Cost Reduction
- Design Flexibility
- Weight Reduction
- High Stiffness
- Uniform Quality
- Simple Manufacturing
- Without Formwork
LGS Buildings made of LGS Frames, Trusses and Joists:
As a result of all advantages this technology is being successfully used in more and more building applications:
- Residential Buildings
- Modular Buildings
- Prefabricated Modules
- Bathroom Pods
- Warehouses
- Site Offices
- Temporary Accomodations
- Office Buildings
- Roof Trusses
- Customized Applications
Profile Dimensions:
Web Width (w)* | 63 - 300 mm |
Flange (h) | 41 - 75mm |
Return Lip (a) | 0 - 20mm |
Thickness (t) | 0,75 - 2,5mm |
Galvanization | 33ksi - 80ksi |
Steel Grade | G40 - G140 |
Accessories
UMS System Accessories:
UMS Accessory Production Capacity:
- Hanger Clip: 6,500 units/day
- Clip: 40,000 units/day
- Anchor Clip: 40,000 units/day
- Connecting Piece: 10,000 units/day
- Double Spring: 20,000 units/day
- L Bracket: 5,000 units/day
- Bracket: 4,500 units/day
- Suspension Rod: 8,500 units/day